Transforming Visions into Reality: Aluminum Casting Illinois
Grasping the Craft: Professional Tips for Flawless Light Weight Aluminum Casting Results
In the realm of light weight aluminum casting, accuracy and experience are paramount to accomplish flawless outcomes. Mastering the craft needs a precise understanding of the tools and tools at one's disposal, an eager eye for preparing the light weight aluminum alloy to specific specs, and a nimble hand in utilizing optimal spreading methods.
Important Devices and Tools
Aluminum casting requires details tools and equipment to make sure accuracy and efficiency at the same time. Vital devices consist of a crucible, ladle, mold, and furnace. The crucible, normally constructed from graphite or ceramic products, withstands heats required to thaw light weight aluminum. A well-insulated heater with the ability of reaching temperatures over 1200 ° C is important to liquefy the metal. The mold, often made of steel or sand, shapes the molten light weight aluminum right into the wanted kind. A ladle is made use of to move the fluid metal from the crucible to the mold without splilling.
In addition, tools like aprons, tongs, and gloves are necessary to guarantee the safety of operators functioning with molten aluminum. Investing in top notch tools and equipment not just enhances the precision of aluminum casting but additionally contributes to a more risk-free and efficient manufacturing procedure.
Preparing the Aluminum Alloy
To ensure the success of the aluminum casting process, precise prep work of the alloy is paramount. The very first step in preparing the aluminum alloy is to very carefully select the appropriate kind of aluminum based upon the characteristics needed for the end product. Aspects such as toughness, corrosion resistance, and machinability need to be taken into consideration when choosing the alloy. As soon as the alloy type is identified, it is important to correctly clean up the aluminum to get rid of any type of pollutants that can influence the casting high quality. This can be done via methods like filtering, fluxing, and degassing.
After cleansing, the following critical step is to heat the light weight aluminum to the proper temperature for spreading. This procedure, understood as alloy melting, ensures that the light weight aluminum remains in its molten form and all set for casting (aluminum casting illinois). Additionally, controlling the temperature during melting is important to avoid getting too hot or underheating, which can result in flaws in the last product. In general, precise preparation of the light weight aluminum alloy establishes the foundation for a successful casting procedure and high-quality end outcomes.
Optimal Casting Strategies
Carrying out accurate casting methods is necessary for achieving top notch results in aluminum casting procedures. One critical technique is making sure correct mold prep work. This entails thorough cleansing and layer of the mold to avoid aluminum from sticking and ensure smooth casting. Additionally, regulating the pouring temperature is vital. The light weight aluminum ought to be heated up to the optimal temperature to decrease flaws like contraction and porosity in the final actors.
Additionally, keeping consistent pouring speed and stress is crucial to achieving harmony in why not try these out the cast item. Slow and stable putting helps protect against turbulence and air entrapment, which can lead to flaws. An additional important element is making use of degassing representatives to eliminate pollutants and gases from the molten light weight aluminum, leading to a cleaner final product.
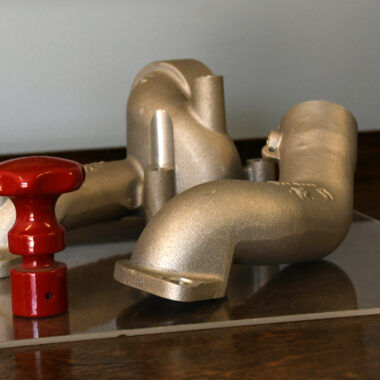
Achieving Smooth Surface Area Completes
For manufacturers looking for to boost the visual charm and high quality of their light weight aluminum spreadings, achieving smooth surface finishes is an important aspect adhering to exact casting techniques and correct cooling treatments. One secret method to attain smooth surface area coatings is by utilizing high-grade mold and mildews that are properly prepared and preserved. The mold and mildew surface area should be carefully cleansed and coated with launch representatives to prevent blemishes moving onto the cast light weight aluminum throughout the cooling procedure.
Moreover, controlling the air conditioning rate of the aluminum casting is essential for achieving a smooth surface coating. Fast cooling can cause thermal gradients that result in appear flaws, while sluggish air conditioning may create microstructural problems - aluminum casting illinois. By executing regulated air conditioning procedures, such as making use of air or water quenching techniques, makers can guarantee that the aluminum solidifies uniformly, decreasing the chance of surface area flaws
Along with mold quality and cooling treatments, post-casting therapies like shot blasting or chemical etching can better improve the surface finish of light weight aluminum spreadings. These strategies assist smoothen out any kind of continuing to be roughness or contaminations, leading to a remarkable appearance that meets the best quality requirements.
Quality Control and Troubleshooting
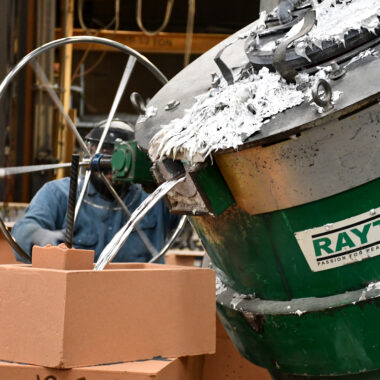
In the realm of troubleshooting, it is crucial to have a thorough understanding of common flaws that can occur during light weight aluminum spreading, such as surface, porosity, or contraction irregularities. By conducting origin analysis and carrying out rehabilitative procedures, suppliers can avoid these issues from persisting in future casting runs. Efficient repairing not just enhances the overall top quality of actors go to the website light weight aluminum products but additionally boosts procedure effectiveness and decreases manufacturing expenses. Continuous improvement via quality assurance and troubleshooting methods is fundamental to Read Full Article attaining remarkable lead to aluminum spreading.
Conclusion
In conclusion, understanding the craft of aluminum casting calls for essential devices and equipment, correct prep work of the light weight aluminum alloy, ideal spreading strategies, accomplishing smooth surface finishes, and applying quality control procedures. By complying with these specialist suggestions, remarkable outcomes can be accomplished in aluminum spreading procedures. Quality assurance and troubleshooting are vital aspects to take into consideration to make sure high-grade and consistent cause light weight aluminum spreading projects.
The first step in preparing the light weight aluminum alloy is to thoroughly choose the appropriate type of aluminum based on the qualities required for the last product.Applying specific spreading strategies is necessary for accomplishing top quality results in aluminum spreading processes. By mastering these optimal spreading strategies, producers can constantly generate remarkable light weight aluminum spreadings.
For suppliers seeking to improve the visual allure and high quality of their light weight aluminum castings, achieving smooth surface finishes is an indispensable facet complying with precise spreading techniques and correct cooling treatments.In verdict, mastering the craft of light weight aluminum casting requires essential tools and equipment, proper preparation of the aluminum alloy, ideal spreading techniques, attaining smooth surface area coatings, and implementing quality control procedures.